CNC Machining Surface Finishing Costs: A Hidden Factor
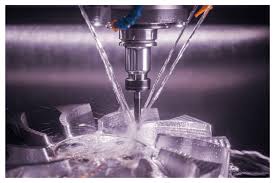
When you think about CNC machining costs, you probably focus on the cutting and shaping processes. But here’s the thing, what happens after the parts are machined can hit your budget just as hard. Surface finishing steps like polishing, painting, heat treating, and surface finishing often add significant hidden costs that many don’t see coming.
If you’re planning a CNC machining project, understanding these extra steps isn’t just smart, it’s necessary. In this article, you’ll discover why post-processing costs matter, what factors drive them up, and how you can make more cost-effective choices without sacrificing quality.
The Significance of Surface finishing in CNC Machining
When your part comes off the CNC machine, it’s not exactly ready for delivery. Raw CNC machined parts often need polishing, coating, deburring, or heat treatment before they meet industry standards. That’s where post-processing steps in. It’s not just about looks, post-processing enhances durability, precision, and performance. Yet many overlook this phase, leading to unexpected costs and project delays. If you want a finished product that’s functional and flawless, post-processing is non-negotiable. Understanding its role early in your planning can save you from last-minute headaches (and expenses) later on.
What Constitutes Surface finishing in CNC Machining
Surface finishing covers all the finishing work done after the CNC machine stops cutting. This includes deburring sharp edges, surface polishing, sandblasting, anodizing, heat treating, and even painting or powder coating. Sometimes, parts also go through precision inspections and adjustments to meet strict tolerances. Each extra step adds time, labor, and materials—meaning extra costs. Depending on your project needs, post-processing can be minimal or highly detailed, but either way, it’s a critical phase you can’t afford to ignore.
Why Surface finishing Costs Are Often Overlooked
Surface finishing costs tend to fly under the radar because they’re not always itemized upfront. Many manufacturers focus quotes on machining time and raw material costs, assuming you’ll handle finishing separately—or simply not mentioning it until later. Plus, clients often underestimate how demanding some finishes can be, especially for aerospace, medical, or automotive parts. Without factoring these in early, you can end up with a budget blowout or compromises in quality. Knowing what’s needed from the start helps you stay on track.
How Surface finishing Affects Your Project Timeline
Surface finishing isn’t just about money—it affects how fast you get your parts. Processes like heat treatment or custom coatings can add days or even weeks to lead times. If you don’t plan for this, you risk missing deadlines or scrambling for rush services, which usually cost even more. Early communication with your machining partner about post-processing needs can streamline your production schedule and avoid last-minute surprises.
Types of Surface finishing Operations and Their Costs
Surface finishing isn’t a one-size-fits-all job. Different operations come with different price tags depending on complexity, labor, materials, and even environmental rules. Let’s break down the most common ones and what you can expect to spend.
-
Deburring and Edge Finishing
Fresh off the CNC machine, most parts have sharp edges, burrs, or rough surfaces that need smoothing. Deburring not only improves appearance but also prevents safety issues and assembly problems later.
Manual vs. Automated Deburring Methods
Manual deburring uses handheld tools, files, or abrasive pads. It’s low-cost but labor-intensive and slower—best for simple parts or small batches. Automated deburring, on the other hand, uses machines like tumblers, vibratory finishers, or robotic arms. While the upfront cost is higher, it’s faster and more consistent, making it ideal for large-scale production.
Cost Comparison of Different Deburring Techniques
- Manual Deburring: ~$5–$15 per part depending on complexity.
- Vibratory Finishing: ~$0.50–$3 per part but requires machine investment.
- Robotic Deburring: Highest setup cost, but $0.10–$1 per part for high volumes.
Choosing the right method depends on your part quantity, precision needs, and budget.
-
Heat Treatment
Heat treatment changes the metal’s properties, like hardness, toughness, or ductility, to match your application needs.
Types of Heat Treatments (e.g., Annealing, Tempering)
- Annealing: Softens metal, improves ductility.
- Tempering: Reduces brittleness after hardening.
- Hardening: Increases surface hardness and wear resistance. Each method requires controlled heating and cooling processes that vary in time and temperature.
Equipment and Process-Related Costs of Heat Treatment
Heat treatment costs include furnace usage, energy consumption, skilled labor, and sometimes protective atmospheres (like vacuum or inert gases). Expect:
- Basic Heat Treatments: ~$50–$150 per batch.
- Specialized Treatments (e.g., vacuum hardening): ~$300+ per batch. Complex parts needing multi-stage treatments naturally drive up the cost.
-
Surface Treatment
Surface treatments boost durability, corrosion resistance, and aesthetics. They can be simple coatings or multi-layered systems.
Painting, Powder Coating, and Their Cost Structures
- Painting: ~$50–$100 per part for industrial-grade coatings. Quick and versatile but less durable.
- Powder Coating: ~$75–$150 per part. Offers better resistance to wear and corrosion, but requires an oven cure. Both depend heavily on part size, surface prep requirements, and color or finish customizations.
Environmental and Regulatory Considerations in Surface Treatment Costs
Many surface treatments must meet environmental standards, like restricting volatile organic compounds (VOCs) in paints or managing waste disposal from coatings. Compliance with regulations like RoHS or REACH can add costs for safer materials, filtration systems, and reporting requirements—sometimes increasing prices by 10–20%.
Factors Affecting Surface finishing Costs
Surface finishing costs in CNC machining aren’t fixed — they vary widely depending on several factors. Understanding these cost drivers can help manufacturers optimize workflows and minimize hidden expenses.
Part Complexity
-
How Complex Geometries Increase Surface finishing Difficulty and Cost
Intricate designs with tight tolerances, deep cavities, or delicate features demand more meticulous post-processing. Complex parts often require manual deburring, custom fixturing during surface treatments, and careful heat application, all of which drive up costs.
-
Strategies to Simplify Surface finishing for Complex Parts
Design for manufacturability (DFM) principles can reduce post-processing challenges. Simplifying features, standardizing radii, and minimizing sharp internal corners can speed up finishing steps and lower overall post-processing costs.
Quantity of Parts
-
Economies of Scale in Surface finishing
Larger production runs significantly reduce the cost per part in post-processing. Automated systems like vibratory deburring machines or batch heat treatment ovens become more cost-effective when processing many parts simultaneously.
-
Cost-per-Unit Variations with Production Volume
Small batches typically see higher post-processing costs per part due to setup times and manual labor. In contrast, high-volume orders allow costs to spread across many parts, lowering the unit price and improving profitability.
Integrating Surface finishing into Cost Estimation
Ignoring post-processing during the quoting phase can lead to unpleasant surprises later. Smart manufacturers factor it in from the start to protect margins and avoid project delays.
Importance of Accurate Surface finishing Cost Projection
-
How Inaccurate Estimates Can Affect Profit Margins
Underestimating post-processing costs eats directly into profit margins. Unexpected expenses from extra finishing steps, manual rework, or regulatory compliance can turn a profitable job into a loss.
-
Tools and Methods for Estimating Surface finishing Costs
Modern quoting software, historical job data, and consultation with finishing experts help create more reliable post-processing cost estimates. Including setup time, labor, equipment wear, and material costs ensures better forecasting.
Collaboration between Machining and Surface finishing Departments
-
Streamlining Communication to Optimize Surface finishing Costs
When machinists and post-processing teams work in silos, mistakes and inefficiencies creep in. Clear communication about surface finish requirements, tolerances, and timelines can prevent costly rework and bottlenecks.
-
Joint Process Optimization for Cost Savings
Early collaboration allows teams to tweak machining parameters or part designs to simplify post-processing. For example, adjusting a machining path to reduce burrs can lower finishing time, saving money on both sides.
Conclusion
Surface finishing costs in CNC machining are often hidden but have a major impact on final project expenses and profitability. From deburring and heat treatment to surface finishing, every step adds value and cost. Understanding these factors, accurately estimating them early, and fostering better collaboration between machining and finishing teams can lead to smoother operations and better profit margins. For manufacturers and buyers alike, being proactive about post-processing isn’t just smart—it’s essential for staying competitive.