Enhancing Efficiency, Quality, and Cost-Effectiveness for Thermoforming
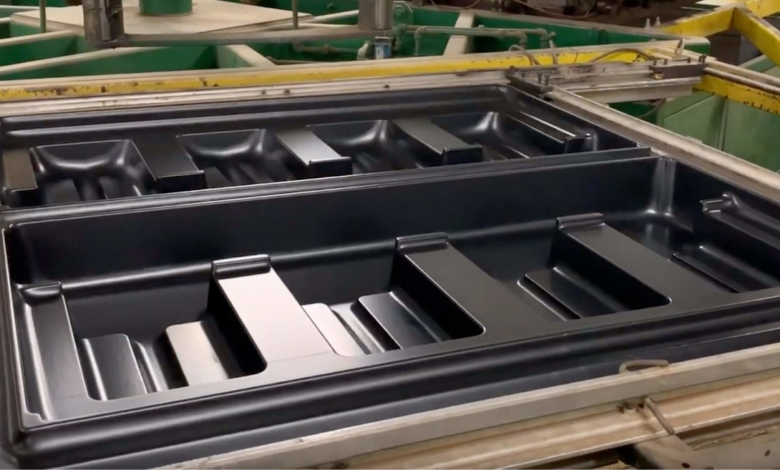
Thermoforming is a widely used manufacturing process for shaping plastic sheets into durable, lightweight, and cost-effective components. It is commonly used in industries such as aerospace, medical, automotive, and consumer goods, where scalability and affordability are key concerns. However, due to the nature of the thermoforming process—where a plastic sheet is heated, formed over a mold, and trimmed—specific design considerations must be made to ensure manufacturability, quality, and production efficiency.
Design for Manufacturability (DFM) principles help engineers and manufacturers optimize thermoforming by addressing key factors such as draft angles, mold selection, material thinning, undercut challenges, and multi-up tooling strategies. By following these best practices, companies can improve product quality, minimize defects, and reduce overall costs.
1. Key Design Principles for Thermoforming
1.1 The Importance of Draft Angles in Thermoforming
Draft angles play a crucial role in ensuring that the formed plastic part can be released from the mold without sticking or deforming. If a part does not have enough draft, it may become trapped, leading to defects or even mold damage.
The required draft angle varies based on the type of mold:
- Male (Positive) Molds – In this case, the mold forms the inside of the part. A draft angle of 3–5° is recommended to accommodate material shrinkage.
- Female (Negative) Molds – Here, the mold forms the outside of the part. Since the plastic naturally shrinks away from the mold, only 1–2° of draft is typically required.
By incorporating proper draft angles into the design phase, manufacturers can prevent costly defects and streamline the production process.
1.2 Male vs. Female Molds: How They Affect Material Thinning
One of the most critical considerations in thermoforming is how the plastic material will stretch and thin during forming. The decision to use a male (positive) mold or a female (negative) mold directly affects this outcome.
- Male Molds (Positive Molds)
- Provide better material distribution, reducing the likelihood of excessive thinning.
- Tend to be more cost-effective to manufacture.
- The final surface texture is determined by the plastic sheet itself, not the mold.
- Female Molds (Negative Molds)
- Allow for more precise external feature details, making them ideal for aesthetic applications.
- More prone to material thinning, as the plastic is stretched into the mold cavity.
- Preferred when high external accuracy is required, such as in automotive or consumer product applications.
Choosing the right mold type is essential to balancing cost, strength, and visual appeal in thermoformed products.
1.3 Handling Undercuts and De-Molding Challenges
Undercuts are features in a part that make it difficult or impossible to remove from the mold without damage. While undercuts add complexity to the manufacturing process, they are sometimes necessary for functional or aesthetic reasons.
To overcome de-molding challenges, manufacturers can use:
- Collapsible Molds – These molds contain moving sections that retract, allowing the part to be released without damage. However, they increase tooling costs.
- Strategic Drafting – If one side of a mold has an undercut, the opposite side can be drafted at a steeper angle to assist in part release.
For thin-gauge plastics, minor undercuts may be feasible, but designers must carefully consider how they impact material stretching and overall part integrity.
1.4 Multi-Up Tooling: Improving Cost Efficiency
One way to significantly reduce production costs is by forming multiple parts from a single plastic sheet. This strategy, known as multi-up tooling, improves material utilization and throughput.
Tooling Type | Parts per Cycle | Production Efficiency |
1-up Tooling | 1 | Best for low-volume production |
2-up, 4-up Tooling | 2–4 | Reduces labor and per-unit costs |
8-up, 16-up Tooling | 8+ | Maximizes material efficiency for high-volume runs |
For example, if a machine forms 5 sheets per hour, a 1-up tool produces 5 parts per hour, while a 4-up tool produces 20 parts per hour, reducing labor costs by 75%. By optimizing the number of parts formed per cycle, manufacturers can dramatically lower overall production costs.
2. Material Thinning and Draw Ratios
2.1 Understanding Draw Ratios and Their Impact on Thickness
The draw ratio is an important factor in thermoforming, as it determines how much a plastic sheet will stretch during the forming process.
Draw Ratio=Part Depth (Z)Minimum Width (X) or Length (Y)\text{Draw Ratio} = \frac{\text{Part Depth (Z)}}{\text{Minimum Width (X) or Length (Y)}}
To maintain part integrity, manufacturers should follow these general guidelines:
- 1:1 or lower – Ideal for preserving uniform thickness.
- 4:3 – The upper limit for standard thermoforming before defects arise.
- Above 4:3 – Likely to result in excessive thinning and weak spots.
If a design exceeds these limits, the use of plug assists—which pre-stretch the plastic before final forming—can help reduce thinning and improve material distribution.
2.2 Estimating Final Part Thickness
Since plastic naturally thins out as it stretches over a mold, designers must account for this effect in their material selection.
Final Thickness=Starting ThicknessDraw Ratio\text{Final Thickness} = \frac{\text{Starting Thickness}}{\text{Draw Ratio}}
For example, if a 0.125” (3.2mm) sheet is formed into a part with a 2:1 draw ratio, the thinnest areas will measure around 0.062” (1.6mm). This can affect the mechanical strength and performance of the final product.
3. Optimizing Cost and Production Efficiency
3.1 Minimizing Material Waste
Plastic waste is a major cost factor in thermoforming. The following strategies can improve material efficiency:
- Optimized Nesting – Arranging parts efficiently on a sheet to maximize yield.
- Custom Sheet Orders – Using non-standard sheet sizes to reduce excess material.
- Adjustable Forming Windows – Customizing forming areas to match part size.
By carefully planning material usage, manufacturers can reduce scrap rates and lower overall costs.
3.2 Trimming and Finishing for Precision
Post-forming trimming ensures parts meet dimensional and aesthetic requirements.
Trimming Method | Best For | Limitations |
CNC Trimming (3-Axis/5-Axis) | High precision, complex geometries | Higher cost |
Hand Trimming | Low-volume runs, simple cuts | Lower precision |
Die Cutting | Thin-gauge, high-volume parts | Limited to 2D cuts |
4. Enhance Your Thermoforming Process with RapidMade
At RapidMade, we specialize in custom thermoforming solutions tailored for a wide range of industries. Our expertise in DFM, high-precision tooling, and material optimization ensures that your parts are manufactured efficiently, cost-effectively, and with superior quality.
Contact us today to discuss your thermoforming project!
Email: info@rapidmade.com
Website: rapidmade.com
With RapidMade, you gain a trusted partner dedicated to improving your manufacturing efficiency and product performance.